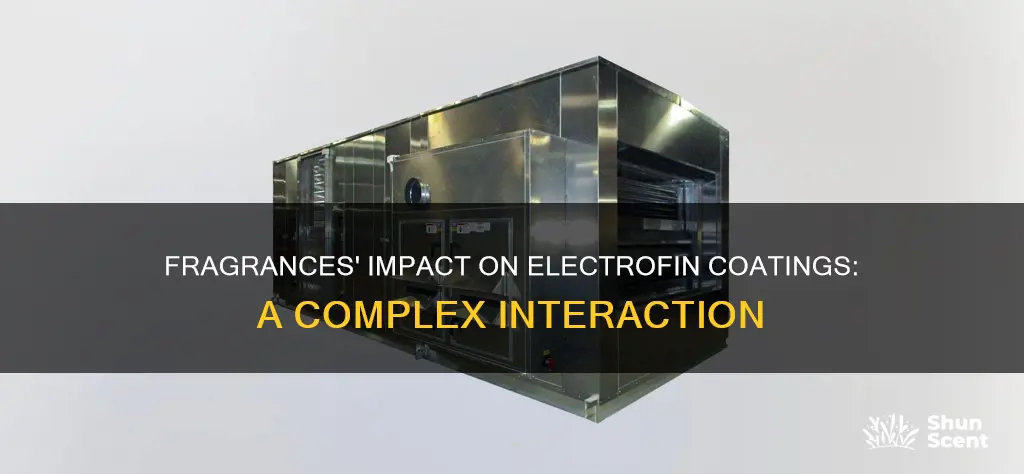
ElectroFin® is a factory-applied electro-deposition coating process that guarantees complete heat exchanger coverage. The coating process involves electrically charging an assembled coil, then submerging it into an oppositely charged bath of water and paint solids. The coil then attracts the coating to every surface, resulting in a thin, flexible, durable, corrosion-resistant layer. While ElectroFin® is suitable for most environmental conditions, it is not recommended for high concentrations of certain chemicals, including nitric acid, sodium hypochlorite, formic acid, hydrofluoric acid, and sulfuric acid. Given the nature of fragrances, further research is required to determine whether they can break down ElectroFin® coatings.
What You'll Learn
What is ElectroFin?
ElectroFin® is a factory-applied electro-deposition coating process that guarantees complete heat exchanger coverage. The coil is immersed in a bath—a mixture of 80-90% deionized water and 10-20% paint solids. The coil acts as a magnet, attracting the coating to every surface. The result is a thin, flexible, durable, and corrosion-resistant coating.
ElectroFin® is designed to protect heat transfer coils from corrosion. These coils are primarily made of aluminium and copper and are used in HVAC/R and electrical power systems. The coating process involves epoxy paint particles that are evenly suspended in deionized water. When electrically charged, the paint particles migrate to and bond with the metal surfaces.
The ElectroFin® coating process is unique in that it provides 100% coverage of coil surfaces, including all edges and cracks. This is in contrast to other coating processes that may fail to cover the entire surface, especially in structures such as microchannel or round tube plate coils. The ElectroFin® coating also includes an extra UV-resistant top coat layer applied by spray to protect the coat from UV and ensure durability and longevity.
The benefits of ElectroFin® include 100% coverage of coil surfaces, maximum uniformity of coating, no loss of operational efficiency, reduced maintenance and operating costs, and extended heat exchanger life.
The Art of Layering Fragrances: A Guide to Creating Your Signature Scent
You may want to see also
How is it applied?
The application of ElectroFin® E-Coat involves a multi-step process, which begins with a thorough inspection of the unit to be coated. This includes checking for any damages or residues that may hinder the adhesion of the coating. Once approved, the unit is tagged with a unique identification number for tracking purposes throughout the coating process and beyond.
The next step is to cover or mask all portals, tubes, and inlets to prevent any chemicals from entering the system during the subsequent steps. If the unit contains a gas charge, it is depleted at this stage and will be refilled before final packaging. The unit is then loaded onto a specialised load bar and prepared for the initial washing process, where it is cleaned with an alkaline solution to remove any dirt, oils, dust, or metal deposits.
Following the washing process, the unit undergoes a two-stage rinsing process, with the first stage heated and the second at ambient temperature, before entering the e-coat tank. The e-coating process is proprietary to ElectroFin® and involves a unique unit grounding technique that ensures complete coverage of the coil. The e-coat bath consists of a mixture of deionized water (80-90%) and paint solids (10-20%), with the paint particles electrically charged to attract and bond with the metal surfaces of the heat exchanger coils. This process is computer-controlled to ensure all areas are adequately covered.
After removal from the e-coat bath, the unit undergoes a visual inspection and is then spray-rinsed to eliminate any loose paint particles. It is then ready for the curing process, which takes place in a drying chamber that gradually reaches optimal temperatures. This curing process results in the formation of a smooth, hard shell that resists corrosion, pitting, and flaking.
Once the curing is complete, the unit is inspected to ensure that all e-coating is properly cured and dry. At this stage, an optional UV-resistant top coat can be manually applied using a spray gun to enhance protection against UV radiation and prolong the life of the coating. A final inspection is conducted to check for any issues, after which the unit is repackaged and returned to the original equipment manufacturer (OEM) for incorporation into the final product.
Yuzu Fragrances: Are They Safe to Use?
You may want to see also
What are the benefits?
The benefits of ElectroFin® coatings are numerous, especially in harsh environments. Firstly, they facilitate thermal transfer while protecting the components from corrosion and impacts, thus maximising the service life of coils in dehumidifiers, HVAC systems, and heat exchangers. This leads to reduced maintenance, replacement, and operating costs.
ElectroFin® coatings are also flexible, durable, and highly uniform, ensuring 100% coverage of coil surfaces, including all edges and cracks. This is particularly beneficial for complex structures such as microchannel or round tube plate coils, where other coating processes may fail to cover the entire surface adequately.
The ElectroFin® coating process is highly specialised, utilising deep cleaning of the coil followed by a proprietary e-coating process with PPG POWERCRON® and a unique curing process. This results in a micro-thin, yet hard and flexible coating that resists corrosion, pitting, and flaking.
The ElectroFin® E-Coat is also an excellent option for coastal and offshore environments, as well as industrial areas with high humidity and aggressive atmospheres. It is internationally recognised as a premier coating solution, providing the highest level of corrosion protection available from an electro coating provider.
While the process may be more expensive and time-consuming than some alternatives, the long-term benefits of extended coil life and reduced maintenance costs make ElectroFin® coatings a worthwhile investment.
Beware Counterfeit Fragrances: Are Larger Sizes a Red Flag?
You may want to see also
What are the drawbacks?
While ElectroFin® coatings are an effective way to protect coils from corrosion, there are some drawbacks to the process. Firstly, it is a more expensive option compared to pre-coated finstock. The process also requires the coil to be shipped to a specialised facility, coated, and then shipped back, adding to the lead time and overall cost.
Additionally, ElectroFin® coatings are hydrophobic, making them unsuitable for applications where the presence of beaded water could have negative effects, such as in evaporators. The coatings can also result in a minor loss of heat transfer efficiency, usually less than 5%protection against a wide range of chemicals and pollutants, they are not suitable for high concentrations of certain substances, including nitric acid, sodium hypochlorite, formic acid, hydrofluoric acid, sulfuric acid, and sodium hydroxide.
Furthermore, the application of ElectroFin® coatings requires rigorous surface preparation and cleaning. Any mistakes or inadequate coverage during the coating process can result in a waste of time and money. Improper maintenance and cleaning, including the use of certain types of cleaners, can also damage the coating over time.
Creed Perfume: How Much Is Too Much?
You may want to see also
How does it compare to other coatings?
The ElectroFin® E-Coat process is a proprietary technology that can only be applied at specific facilities. It is a unique process that provides an electro-deposition coating, involving epoxy paint particles evenly suspended in deionized water. This is unlike other coating processes, which may involve manual dipping or spraying, leading to surface imperfections and inconsistent thicknesses.
The ElectroFin® process is also specifically designed for heat transfer coils, whereas other coating processes may be used for a wider range of applications, such as radiators, auto parts, and various other metal components. This specialization allows the ElectroFin® process to optimize its coating for heat transfer coils, resulting in a more effective and efficient coating.
The ElectroFin® E-Coat process is internationally recognized and offers several advantages over other coating methods. Firstly, it guarantees complete and uniform encapsulation with 100% coverage, ensuring that the coating penetrates into all coil cavities and covers the entire coil assembly. This level of protection is not always achievable with other coating methods, which may leave microscopic holes or areas of incomplete coverage.
Secondly, the ElectroFin® process results in a smooth, consistent, and flexible coating that is less brittle and more durable. This is due to the unique properties of the coating material and the controlled application process. The coating thickness can be regulated by adjusting the applied voltage, ensuring that the coating is uniformly micro-thin, yet hard and flexible.
In addition, the ElectroFin® E-Coat process utilizes a deep cleaning step before coating, which is crucial for ensuring reliable bonding between the metal and the coating. This step is often not included in other coating processes, particularly spray field applications.
Furthermore, the ElectroFin® E-Coat process is specifically designed for heat transfer coils manufactured primarily from aluminum and copper for the HVAC/R and electrical power systems industries. This specialization allows for optimized protection in severe environments, such as coastal and offshore areas with high humidity and aggressive atmospheres.
Overall, the ElectroFin® E-Coat process offers superior protection, flexibility, and durability compared to other coating methods. It is a trusted and internationally recognized process that has been successfully applied to hundreds of thousands of heat transfer coils globally, with a 5-year warranty provided.
Fragrance: Is It Harmful to Your Health?
You may want to see also
Frequently asked questions
ElectroFin is a factory-applied electro-deposition coating process that guarantees complete heat exchanger coverage. The coil is immersed in a bath, attracting the coating to every surface. The result is a thin, flexible, durable, corrosion-resistant coating.
ElectroFin offers 100% coverage of the coil surface, maximum uniformity of coating, no loss of operational efficiency, reduced maintenance and costs, and an extension of the heat exchanger's life.
The ElectroFin coating process involves deep cleaning of the coil, followed by a proprietary e-coating process and a curing process. The coil is electrically charged, submerged in a bath of oppositely charged water and paint solids, rinsed, and oven-baked, resulting in a hydrophobic coat.
Fragrances are not mentioned in the list of chemicals that ElectroFin coatings are not suitable for. However, it is important to note that the effectiveness of coatings can vary depending on the specific chemicals and fragrances present. It is recommended to consult with the coating manufacturer to ensure the coating is compatible with the specific environment and substances it will be exposed to.